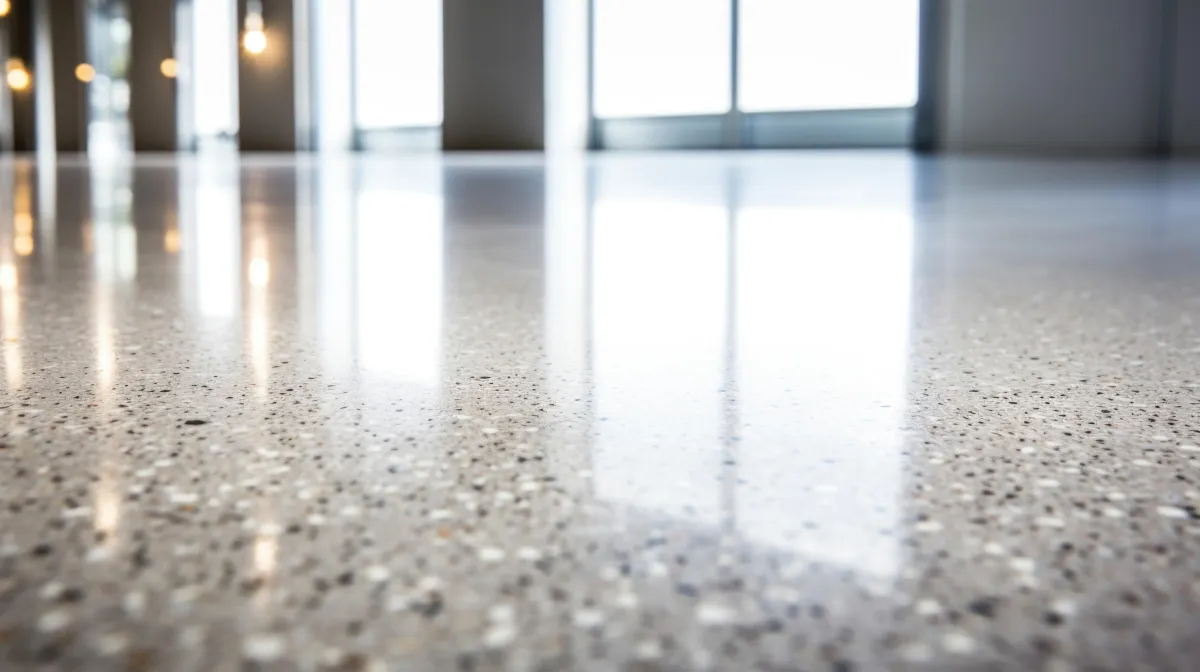
Polished Concrete vs. Tile: What’s the Better Choice for Arkansas Homes and Businesses?
Flooring That Fits Arkansas Living
Whether you're remodeling your home in Little Rock or finishing out a new commercial space in Benton or North Little Rock, choosing the right flooring is a bigger decision than most people realize. The wrong floor can turn into a maintenance headache, while the right one can save you thousands over the years—not to mention look great doing it.
Two of the most common choices we hear about at Rock City Epoxy are tile and polished concrete. Tile has been the go-to for decades—especially in kitchens, bathrooms, and retail—but polished concrete has exploded in popularity across Arkansas for good reason. It’s sleek, tough, low-maintenance, and surprisingly customizable.
But which one is actually better?
The truth is, they each have strengths—but the best choice depends on where you’re installing it, what kind of foot traffic it’s going to get, and how much upkeep you’re willing to deal with long-term.
In this post, we’re going to break it all down: the pros, the cons, the hard truths. If you're in Central Arkansas and considering a flooring upgrade for your home, office, shop, or showroom, this guide will give you the real-deal info you need to make the right call.
Let’s dig into what makes polished concrete and tile so different—and why one might make a whole lot more sense for your space.
Overview of Each Option
When you’re deciding between polished concrete and tile, it helps to understand what each one actually is—not just how they look, but how they’re built and installed. These two materials behave very differently under pressure, and knowing what you’re working with from the start will save you from unexpected issues down the road.
What Is Polished Concrete?
Polished concrete isn’t just regular concrete with a little shine—it’s a finely tuned surface that’s been mechanically ground, hardened, and polished using specialized equipment and techniques. The process involves multiple passes with diamond abrasives, often starting with a coarse grind to remove imperfections and ending with a high-grit polish that gives the floor its signature sheen.
During the polishing process, a densifier is applied to harden the surface and reduce dusting. You can customize the look through different gloss levels (from satin to mirror-like), color dyes, exposed aggregate finishes, and saw-cut patterns. And because the system works with the concrete that’s already there, it’s ideal for both residential remodels and large-scale commercial projects in Little Rock and surrounding areas.
The result? A seamless, durable, and easy-to-clean floor that’s as functional as it is modern.
What Is Tile Flooring?
Tile is a more familiar option for most homeowners. It includes materials like ceramic, porcelain, and natural stone, each available in a wide range of styles, sizes, and finishes. The tiles are installed over a backer board or slab using mortar, with grout filling the gaps between them.
Porcelain tile is one of the more popular choices in Arkansas because of its durability and low water absorption rate—especially in kitchens, bathrooms, and entryways. Ceramic tile tends to be a bit more affordable and easier to cut, but it’s also more prone to cracking under stress. Natural stone tile (like travertine or slate) brings a unique, high-end aesthetic but often requires sealing and more ongoing maintenance.
Unlike polished concrete, which creates one continuous surface, tile is installed piece by piece—and every grout line becomes a potential weak point over time.
Durability: What Holds Up in Real Life
When it comes to flooring in Arkansas homes and businesses, durability isn’t just a nice-to-have—it’s the make-or-break factor. Whether you’ve got a house full of kids and pets or you’re running a busy commercial shop, your floor needs to stand up to daily punishment without cracking, chipping, or becoming a maintenance nightmare. This is where the differences between polished concrete and tile really start to show.
Polished Concrete: Built to Take a Beating
Polished concrete is the kind of surface that shrugs off abuse. It’s densified and hardened during the grinding process, which means it can take on everything from dropped tools to heavy rolling loads without flinching. In a commercial setting—like a retail space, brewery, or warehouse—a properly installed polished concrete floor can easily last 20 years or more with minimal maintenance.
Even in a home, polished concrete doesn’t wear out from pets running across it, kids dragging furniture, or the occasional mishap in the kitchen. There are no grout lines to crack or tiles to pop loose. If you do get a scuff or mark, it usually buffs out without much fuss. Plus, there’s no risk of delamination because you’re not applying anything on top—it is the floor.
And for businesses in Little Rock that rely on forklifts or pallet jacks? Polished concrete doesn’t even blink. This flooring system is rated to handle serious loads and high-traffic environments without giving out or looking worn down after a few years.
Tile: Strong Until It Isn’t
Tile has a reputation for being tough—but its durability has conditions. Ceramic and porcelain tiles themselves are fairly hard, but they’re also brittle. Drop something heavy (like a wrench or a cast iron pan), and you’re looking at cracks or chips that can’t be buffed out. And unlike polished concrete, which is monolithic, tile is a system of individual pieces, each surrounded by grout—an inherently weaker material.
In commercial spaces, the constant foot traffic and heavy impacts can wear out grout lines quickly. Once grout starts deteriorating, it doesn’t just look bad—it can also allow moisture underneath the tiles, which leads to loosening and lifting. That’s a common failure point we see in older tile floors, especially in places with fluctuating moisture levels like kitchens, bathrooms, and break rooms.
And if your slab underneath shifts even slightly—say from settling soil or temperature swings—you can end up with cracked tiles or uneven spots. In Arkansas, where humidity and freeze-thaw cycles can mess with foundations, that risk is very real.
Bottom Line: Polished Concrete Wins the Long Game
If you’re looking for something that can go the distance with minimal maintenance and fewer points of failure, polished concrete is the clear winner. Tile can look great when it’s new—but it’s not nearly as forgiving when life happens.
Maintenance and Cleaning
Durability is one thing. But let’s talk about what happens after the install—because even the toughest floor becomes a burden if you’re constantly cleaning it or paying to fix problems. This is where polished concrete leaves tile in the dust (literally).
Polished Concrete: Low-Maintenance by Design
Polished concrete is as close to set-it-and-forget-it flooring as it gets. Once the surface has been ground, densified, and polished, there’s nothing sitting on top to peel, chip, or trap dirt. There are no grout lines to scrub, no sealers to reapply every year, and no waxes required to keep it shiny.
Cleaning is as simple as sweeping and mopping. A microfiber pad and a pH-neutral cleaner are usually all it takes to keep it looking great. And if the floor starts to look dull after years of use? A quick re-buff brings it right back to life—no demolition, no tearing up tiles, and no major downtime.
This is a huge advantage for Arkansas businesses where operations can't afford to shut down for a floor redo. Even in homes, especially in open-plan spaces, polished concrete keeps cleaning time (and costs) to an absolute minimum.
Tile: High-Maintenance in All the Wrong Places
Tile’s reputation for being “easy to clean” falls apart once you live with it for a while. Sure, the surface of the tile wipes clean. But the real headache is the grout.
Grout lines are porous and prone to absorbing moisture, grease, dirt, and bacteria. Even with sealing, they eventually discolor—especially in high-traffic areas or wet zones like kitchens, bathrooms, or restaurant floors. Mold and mildew love to hide in those tiny lines, and cleaning them means breaking out the scrub brush and harsh chemicals more often than anyone wants.
And if a tile cracks or chips? You’re not just replacing that one piece. Matching the tile, removing the grout, and redoing the area can turn into a time-consuming—and expensive—repair job.
The Cleaning Verdict
In day-to-day life, polished concrete is simply easier to live with. No grout, no special treatments, no annual resealing schedules. Just a durable surface that stays cleaner, longer. If you’re trying to reduce maintenance in your home or keep cleaning crews efficient in your commercial space, polished concrete makes that job a whole lot easier.
Aesthetic Options and Design Flexibility
Let’s be honest—looks matter. Whether you’re designing a sleek modern kitchen in a Little Rock condo or updating the lobby of your commercial space in Conway, the flooring you choose sets the tone. And while tile has long been known for its visual variety, polished concrete has quietly evolved into one of the most versatile and design-forward flooring options on the market.
Tile: A Familiar Look with Style Limits
Tile brings a sense of tradition. You can find it in every color, pattern, and faux finish under the sun—wood-look planks, marble-look squares, even mosaic patterns. That makes it appealing to homeowners who want a specific visual style right out of the box.
But for all its variety, tile’s appearance is always segmented. Every tile is an individual piece, separated by grout lines that break up the flow of the room. In smaller spaces, this can make the area feel busier or more cramped. And even with patterned layouts or creative transitions, tile still tends to look and feel like... well, tile.
Plus, once you’ve chosen a tile style and laid it down, there’s no changing it without ripping the whole thing up.
Polished Concrete: Seamless and Surprisingly Stylish
This is where polished concrete turns heads. A lot of people still picture gray warehouse floors when they hear “concrete,” but that image is way outdated. Today’s polished concrete offers a huge range of design options:
Gloss levels ranging from matte satin to high-gloss mirror finish
Color dyes and stains in earth tones, bold hues, or custom blends
Exposed aggregate for a terrazzo-like texture
Saw cuts and stencils to create borders, logos, or geometric patterns
Embedded elements like metal strips or decorative glass for a one-of-a-kind look
Because it’s seamless, polished concrete makes spaces feel larger, cleaner, and more modern. There are no visual interruptions from grout lines, no variations between tiles, and no risk of an uneven layout ruining the look.
This minimalist, high-end aesthetic has made polished concrete a go-to choice in modern homes, high-end retail spaces, art galleries, and offices throughout Little Rock. It delivers that “wow” factor while still being incredibly practical.
Design Flexibility That Works Across Spaces
Whether you're designing for functionality or style, polished concrete adapts. Want something understated and industrial? Keep it simple with a matte gray finish. Want something bold? Add a vibrant dye, a gloss finish, and custom scoring to make the floor the centerpiece.
And because it's a finish applied to your existing slab, you’re not limited by stock or supplier availability. Your floor becomes a custom canvas.
Cost Breakdown: Installation and Long-Term ROI
Alright, let’s talk money—because budget is often the deal-breaker when it comes to flooring decisions. But the true cost of a floor isn’t just what you pay upfront. It’s what you spend over the next 10 to 20 years in maintenance, repairs, and replacement. This is where the difference between polished concrete and tile becomes crystal clear.
Upfront Installation Costs: Tile vs. Polished Concrete
Tile typically has a lower starting cost—at least on paper. Basic ceramic tile can be inexpensive, and if you’re doing a small space like a bathroom or kitchen, that price tag might look appealing. But as with most things, the devil’s in the details. Add up the cost of:
Tile itself (higher if you’re using porcelain or stone)
Thinset mortar
Grout and sealers
Underlayment or backer board
Professional installation (which gets pricey fast for large or complex layouts)
Labor drives up tile costs quickly. It’s a slow, hands-on process that requires precision and prep. For a whole-home install or large commercial space in Little Rock, tile pricing can spiral out of control—especially when you add time-sensitive labor and cleanup.
Polished concrete, on the other hand, often comes with a higher initial install cost per square foot—especially if extensive grinding is needed or the slab has issues to fix. But keep in mind: you’re working with the floor you already have. There are no extra materials, no adhesives, no grout, and no tiles to transport or store.
And while polishing is a multi-step process, it’s typically much faster and cleaner than a tile install—especially for open-concept homes or commercial buildings where speed matters.
Lifecycle Costs: Who’s Cheaper Over Time?
This is where polished concrete dominates. Once it’s in, it’s in. There are no grout lines to re-seal, no tile edges to re-grout, and no floor coverings to replace every 7–10 years. Polished concrete can easily last 20+ years with minimal upkeep.
Tile, by comparison, almost always needs some form of ongoing maintenance:
Grout sealing (every 1–2 years)
Spot cleaning and mold removal
Replacing chipped or cracked tiles
Full tear-out and replacement if the subfloor shifts or moisture gets in
In commercial settings, the maintenance bill for tile over a decade often outweighs the initial savings. And in homes, tile repairs are a constant nuisance—especially when the original tile pattern has been discontinued.
Repair and Downtime Costs
Fixing a chipped tile? You’re dealing with a whole mini-renovation. That means dust, demo, and downtime—plus the hassle of trying to match your existing floor if the original tile is no longer available.
With polished concrete, most scuffs or wear spots can be refinished or re-buffed in place—no replacement required, and usually no disruption to your home or business operations.
Return on Investment
Flooring upgrades aren’t just about comfort—they impact property value. Polished concrete has become a selling point in modern homes and is often seen as a premium upgrade in commercial real estate listings. It’s low-maintenance, allergy-friendly, and visually appealing.
Tile has a place, but it doesn’t stand out the way polished concrete does in today’s design-conscious market. If you’re thinking long-term resale or rental value in Little Rock or surrounding areas, polished concrete adds serious curb appeal—without the upkeep costs dragging you down.
Slip Resistance and Safety
When it comes to safety—especially in commercial buildings or high-traffic areas—you can’t afford to roll the dice. The wrong floor in the wrong environment can lead to serious liability issues, not to mention accidents at home. While both polished concrete and tile can be made safer with the right finish or treatment, one definitely gives you more control and reliability.
Polished Concrete: Custom Traction That Works
One of the big misconceptions about polished concrete is that it’s slippery. Sure, if you polish it to a high-gloss mirror finish and spill water on it, yes—it can get slick. But that’s not how most commercial or residential floors are finished.
At Rock City Epoxy, we can dial in the level of grip you need by adjusting the polishing level or adding a fine grit guard during the densification process. That means you can get a surface that looks sleek but still offers solid traction—whether it’s a grocery store entrance, a showroom, or a modern kitchen at home.
And because polished concrete is seamless, you’re not dealing with the little trip hazards that grout lines and uneven tile edges can create. For anyone worried about accessibility, ADA compliance, or just keeping kids and grandparents upright, polished concrete can be tuned to deliver excellent slip resistance.
Tile: Slippery When Wet (and Uneven Over Time)
Tile’s safety story is more hit or miss. Yes, some tiles are textured or come with an anti-slip rating—but not all do. Glossy ceramic or porcelain tiles in bathrooms or entryways can turn into ice rinks when wet. That’s a real issue in Arkansas homes during rainy weather or humid summers when floors sweat.
And then there’s grout. As tile ages and grout starts to deteriorate or wear unevenly, you can end up with subtle height differences between tiles—a tripping hazard most people don’t see coming until it’s too late. In commercial environments, that’s a liability waiting to happen.
Replacing a cracked or lifted tile to fix a safety issue isn’t quick either. You have to demo the area, clean it up, and hope you can match the old tile. Meanwhile, that part of your home or business stays shut down until it’s fixed.
When Safety Is Non-Negotiable
In schools, restaurants, hospitals, and offices—anywhere people are walking all day long—polished concrete with a slip-resistant finish is often the smarter move. It gives you reliable, predictable traction and can be maintained over time without patchwork repairs.
For homeowners, especially families with kids or elderly relatives, a lightly polished or satin finish concrete floor provides both beauty and peace of mind.
Climate & Regional Considerations (Why Little Rock Matters)
You can’t talk flooring without talking climate—especially in a place like Arkansas. Little Rock and the surrounding areas see hot, humid summers, surprise cold snaps, and the occasional flood risk. That mix of moisture, temperature swings, and shifting soils has a big impact on how well your floor holds up over time.
Here’s how polished concrete and tile stack up when it comes to working with—not against—Arkansas’ climate.
Polished Concrete: Made for Southern Conditions
Polished concrete is ideal for areas with wide temperature and humidity swings. Why? Because it doesn’t rely on adhesives, grout, or layered materials that expand and contract differently. It is the slab. No layering means no risk of delamination or shifting, and the floor naturally stabilizes with the building’s structure.
When the summer humidity cranks up, polished concrete stays cool and doesn’t sweat the way tile often does. That’s a win for comfort and slip resistance. During winter, even if the slab gets cold, it doesn’t crack or separate like some tile installations do under freeze/thaw stress.
In homes without perfect climate control—or garages, shops, and commercial spaces that get a lot of outdoor airflow—polished concrete keeps performing year after year, no matter what the Arkansas weather is doing outside.
Tile: Not Built for Slab Movement or Humidity
Tile, unfortunately, doesn’t handle movement well. Even small shifts in the foundation or minor slab cracks can cause individual tiles to pop, crack, or loosen. And if moisture seeps into the grout or underneath the tiles (especially in basements, bathrooms, or kitchens), you’re looking at mold, mildew, or costly repairs.
We’ve seen plenty of homes around Little Rock where tile floors start strong and look great—only to develop hairline cracks or hollow spots after just a few years due to seasonal slab movement or moisture intrusion. That’s not just a cosmetic issue—it’s a structural one that can spread quickly.
In flood-prone areas or places with high ground moisture, tile is a gamble. Unless it’s installed perfectly with waterproofing measures, you may end up with problems hiding underneath the surface.
Built for Arkansas Life
If you’re in a neighborhood with shifting soils, have an older slab that’s not perfectly level, or want a floor that doesn’t flinch at seasonal extremes, polished concrete is the smarter play. It holds up better in the heat, doesn’t crack under pressure, and won’t turn into a breeding ground for mold when the humidity rises.
Sustainability and Eco Impact
Sustainability isn’t just a buzzword—it’s something more and more homeowners and business owners in Little Rock care about. Whether it’s reducing your carbon footprint, minimizing waste, or avoiding toxic materials in your space, the floor you choose can play a big role in your project’s environmental impact.
So how do tile and polished concrete compare when it comes to eco-friendliness? Let’s break it down.
Polished Concrete: Reuse, Reduce, Refine
Here’s the beauty of polished concrete: you’re not adding a new material—you’re refining what’s already there. No tiles. No adhesives. No excess materials needing to be produced, transported, or disposed of later. The process uses your existing concrete slab and enhances it with grinding and polishing equipment, plus densifiers that are typically low in VOCs (volatile organic compounds).
That means fewer emissions from manufacturing, fewer raw materials extracted from the earth, and less waste ending up in landfills. Even better? Polished concrete reflects more light than unfinished floors, which can reduce the need for artificial lighting in commercial settings—lowering your energy bills and your footprint at the same time.
If you're pursuing LEED certification or just trying to make smarter building choices in Arkansas, polished concrete gives you a flooring solution that aligns with green building principles without sacrificing performance or aesthetics.
Tile: More Resources, More Waste
Tile—especially ceramic and porcelain—requires a lot more energy to produce. It’s kiln-fired at extremely high temperatures and often shipped long distances before it ever reaches your site. Natural stone tiles can be even more resource-intensive, depending on where the stone was quarried and how it was finished.
The installation process also creates waste: leftover tiles, cutoffs, packaging, grout containers, and more. And once tile wears out or breaks, there’s really no “recycling” it. It usually ends up in a dumpster, destined for the landfill.
Grout and adhesives used in tile installations may also contain VOCs, especially cheaper products. And while some tiles are labeled as “eco-friendly,” the entire system still carries a higher embodied energy cost than polished concrete.
Looking Ahead
If you’re trying to build smarter—not just for today, but for the future—polished concrete puts you ahead of the game. It’s a leaner, cleaner approach that makes the most of what you already have. No wasteful tear-outs. No chemical-heavy sealants. Just a floor that performs and keeps performing without wrecking your sustainability goals.
Which Is Better for Your Space? Expert Recommendations
After everything we’ve covered—durability, maintenance, design, climate, cost, safety, and sustainability—you’re probably wondering: So which one should I choose?
Here’s the no-BS breakdown.
Choose Polished Concrete If:
You want a long-lasting, low-maintenance floor that won’t need constant upkeep
You’re looking for a modern, seamless look that makes spaces feel clean and expansive
Your space gets heavy traffic, rolling loads, or moisture exposure (think garages, shops, lobbies, kitchens)
You’re dealing with Arkansas’ humid climate, shifting soil, or slab-on-grade construction
Sustainability is a priority and you’d rather refine the existing slab than import more materials
In these scenarios—and we see a lot of them here in Little Rock—polished concrete just makes more sense. It performs better long-term, handles environmental stress without flinching, and looks great doing it.
Go with Tile If:
You’re doing a small-scale update (like a powder room or decorative backsplash)
You need a specific aesthetic that’s only available in a tile pattern or color
You’re working within a tight budget and don’t expect high wear and tear
You’re okay with the idea of more maintenance and eventual repairs
Tile still has a place. For very targeted applications where foot traffic is low and visual impact is more important than long-term durability, it’s a workable option.
But if you’re making a decision for the whole house, a busy commercial space, or any area that sees a lot of use—polished concrete is the smarter, tougher investment.
At Rock City Epoxy, we’ve installed polished concrete in homes, shops, showrooms, and industrial spaces all across Central Arkansas. We’ve seen firsthand how it holds up, how it looks years later, and how happy clients are when they don’t have to worry about cracks, stains, or grout lines ever again.
Let’s Talk About Your Floor
You’ve got options—but not all floors are built to last. Whether you're updating your home, remodeling a commercial space, or starting fresh on a new build, the right floor can make all the difference. At Rock City Epoxy, we’re here to help you get it right the first time.
Polished concrete isn’t just a surface—it’s a long-term solution. We install floors that hold up to Arkansas heat, humidity, traffic, and time. If you’re in Little Rock or anywhere nearby—North Little Rock, Benton, Sherwood, Maumelle, or beyond—we can help you figure out the best system for your space and your goals.
When you work with us, you’re not getting a sales pitch. You’re getting honest advice from a contractor who takes pride in the craft.
Want to learn more or get a free quote?
Call TJ at (501) 408-6160 shoot an email to [email protected] or fill out our contact form
Let’s talk about your project—and make your floor something solid.