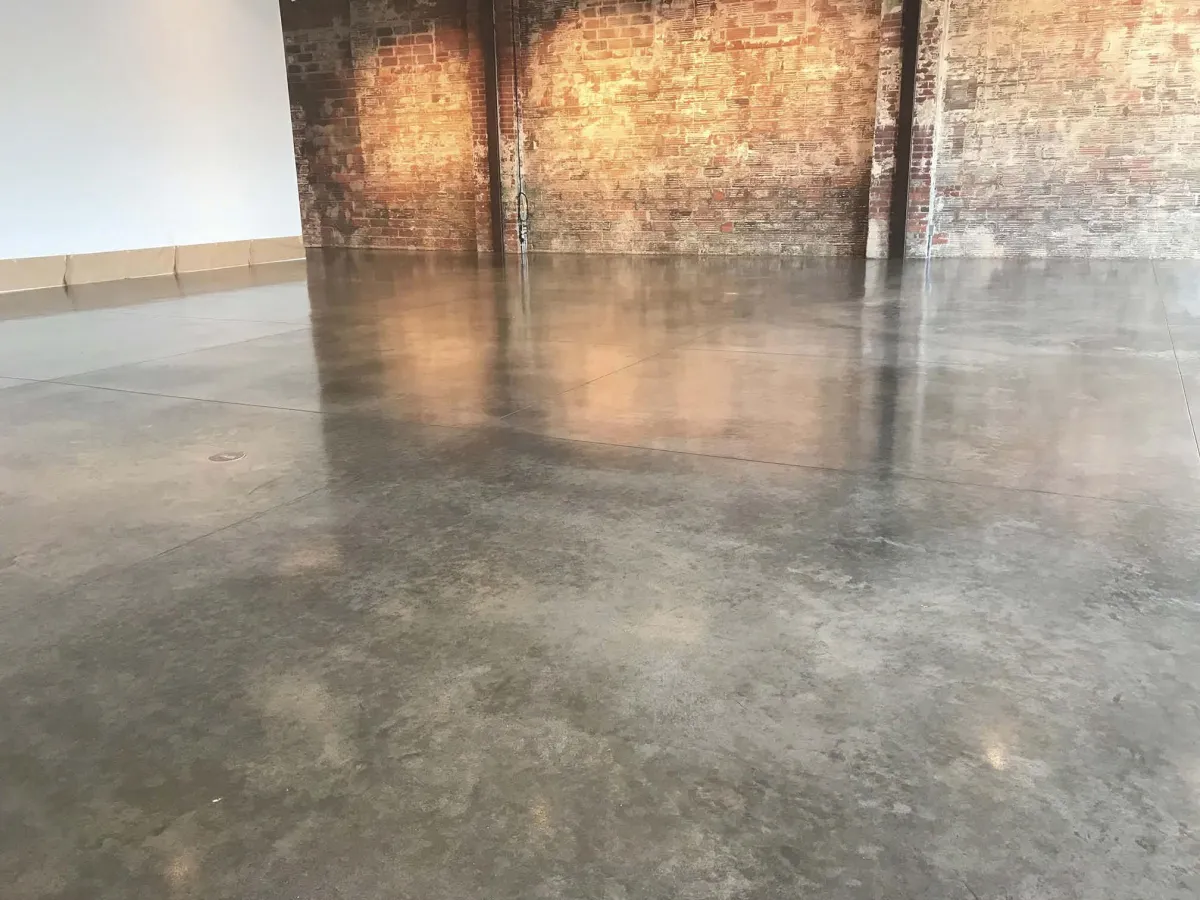
Grind & Seal vs. Polished Concrete: What’s the Difference and Which One Should You Choose in Arkansas?
Concrete Floors Aren’t One-Size-Fits-All
If you’ve been looking into concrete floor finishes for your home or business in Little Rock, chances are you’ve run into two popular options: grind & seal and polished concrete. And if you're like most people, you've probably wondered—aren’t they basically the same thing?
We get this question all the time. And on the surface, it’s understandable. Both processes involve grinding the concrete. Both can create a glossy, modern look. And both are widely used in residential, commercial, and industrial spaces across Arkansas.
But here’s the reality: these two systems are completely different when it comes to performance, longevity, maintenance, and cost over time.
One is a budget-friendly coating system that looks great short-term but requires regular resealing. The other is a mechanically hardened finish that transforms the concrete itself into a dense, polished surface built to last for decades.
Choosing the wrong one can mean redoing your floor in five years. Choosing the right one? That gets you a surface that stays sharp, strong, and low-maintenance for the long haul.
In this post, we’re going to break down everything you need to know—without the industry jargon. Whether you’re planning a renovation in downtown Little Rock, upgrading your garage in Benton, or opening a new retail space in Conway, this guide will help you decide which system is the better fit for your project.
What Is Grind & Seal?
Grind & seal is a concrete finishing system that gives your floor a clean, modern look—without going through the full polishing process. It’s quicker, less expensive, and still delivers a solid upgrade from bare concrete. That makes it a popular choice for garages, basements, retail stores, and even some commercial spaces across Central Arkansas.
How It Works
Here’s the basic breakdown:
Grinding: The concrete surface is mechanically ground to remove surface imperfections, glue, or coatings, and to expose a bit of aggregate if desired. This can be a light grind or a more aggressive pass depending on the look you're going for.
Sealing: After the grinding is done, a topical sealer is applied over the surface. This can be a clear coat or a tinted sealer if you want to add some color to the floor. Sealers come in different finishes—matte, satin, or high-gloss—and they create a protective film over the surface.
Optional Add-Ons: Want to boost durability or slip resistance? Grit additives can be mixed into the sealer to increase traction, especially in wet areas like garages or entryways.
That’s it—grind, seal, done. It’s a fairly quick turnaround and doesn’t require the multiple steps that true polished concrete does.
Where It’s Commonly Used
Grind & seal is often chosen for:
Residential garages and basements where budget is a factor
Retail stores or commercial spaces that want a clean look without a high install cost
Restaurants and bars that like the industrial aesthetic
Short-term renovations or spaces that may be remodeled again within a few years
The look is sleek and modern, and it works well in areas that don’t take a constant beating. But make no mistake—this is a surface coating. The sealer is what gives the floor its gloss and protection, and that layer will wear over time.
What Is Polished Concrete?
Polished concrete isn’t a coating—it’s a transformation. It’s a flooring system that strengthens, refines, and enhances your existing concrete slab through a mechanical process. Where grind & seal stops after the surface is ground and sealed, polished concrete keeps going—layer by layer—until the slab itself becomes the finished floor.
It’s not about adding something on top. It’s about bringing out the natural strength and beauty of the concrete from within.
How It Works
The polishing process is a multi-step system that requires specialized equipment and experienced installers. Here’s how it works:
Initial Grinding: The surface is aggressively ground with diamond abrasives to remove imperfections and flatten the slab. This also determines how much aggregate (stone) gets exposed.
Densifier Application: A liquid densifier is applied to chemically harden the surface. This fills in pores, increases abrasion resistance, and minimizes dusting.
Progressive Polishing: The floor is then polished in multiple passes using finer and finer grits. Think of it like sanding wood—from coarse to ultra-fine—until the floor shines.
Optional Color or Decorative Work: Dyes can be added for color, saw cuts can be made for patterns, and logos or graphics can be embedded during the process.
Final Burnish or Seal (Optional): Depending on the project, the final stage may include a burnishing step or guard coat to enhance shine and stain resistance—though it’s not the primary protection like in a grind & seal system.
Where It Excels
Polished concrete is built for the long haul. It’s a top performer in:
High-traffic commercial spaces like retail, offices, showrooms, and schools
Modern residential interiors that want a seamless, minimalist aesthetic
Industrial and warehouse environments where durability and cleanliness matter
Any space that sees frequent wear, spills, or rolling loads
It doesn’t peel. It doesn’t chip. It doesn’t need to be reapplied every few years. The polish is in the floor—not on it.
Customization Options
Polished concrete offers a wide range of looks—from a natural salt-and-pepper finish to full aggregate exposure with added dye. You control:
Gloss level (matte to mirror)
Color tinting
Aggregate exposure
Patterned cuts or borders
The result is a completely custom, architectural-grade finish that’s as functional as it is beautiful.
Visual Differences: Can You Even Tell?
From a distance, grind & seal and polished concrete can look similar—especially when both are done with a medium to high-gloss finish. And for someone flipping through Pinterest photos or flooring catalogs, it’s easy to get them confused.
But when you know what to look for—and when you see them in person—the differences are clear.
Grind & Seal: Glossy, But With a Coated Feel
Grind & seal gets its shine from a topical sealer—a liquid coating that sits on the surface of the concrete. That sealer creates a plastic-like film over the slab, which can give off a reflective, wet-look finish. It’s slick, it’s clean, and in the right light, it looks sharp.
But up close, the sealer can show minor imperfections:
Brush or roller marks from application
Occasional bubbling if the slab wasn’t fully degassed
A slight “film” feel when you run your hand across the surface
And over time, the sealer can start to dull, haze, or peel—especially in areas that get a lot of traffic or sun exposure. It’s a surface finish, and like any coating, it wears from the top down.
Polished Concrete: Glassy, Stone-Like Surface
Polished concrete, on the other hand, gets its finish from within the slab itself. After the densifier hardens the surface, the polishing process reveals a smooth, dense, stone-like texture that reflects light cleanly—without the need for a topical coating.
When you touch it, there’s no “film” feeling. Just a slick, cool, solid surface that feels like polished stone. It reflects light differently, too—it has more depth and clarity, especially in higher gloss finishes.
There’s no bubbling, no roller marks, and no peeling. What you’re seeing is the actual concrete, not a layer on top of it.
What Clients Notice
Here in Little Rock, we’ve had clients who initially leaned toward grind & seal for budget reasons—until they saw a polished concrete floor in person. The difference in clarity and depth is hard to unsee.
Grind & seal has a nice shine—but polished concrete has a presence.
Durability & Longevity: Which Holds Up Longer?
If you’re investing in a concrete floor finish, you probably don’t want to redo it in five years. And in Arkansas—where we deal with humidity, heat, freeze-thaw cycles, and slab movement—you can’t afford to choose a system that flakes, fails, or needs constant babysitting.
So let’s talk real-world durability: how long these systems actually last, and what kind of abuse they can take.
Polished Concrete: A Long-Term Flooring System
Polished concrete isn’t just hard—it’s hardened. The densifier chemically reacts with the calcium hydroxide in the concrete, turning it into a much denser, abrasion-resistant surface. Then, the multi-step polishing process tightens up the surface even more—creating a floor that can handle years of wear without breaking down.
In a typical commercial setting, a properly installed polished concrete floor can last 15 to 25 years or more. We’ve seen polished concrete in warehouses, airports, and retail stores hold up with nothing more than routine cleaning and the occasional re-buff.
And at home? You’re talking about a floor that shrugs off pet claws, furniture legs, foot traffic, kids' scooters—you name it.
It resists:
Scratches and scuffs
UV damage (no fading or yellowing)
Moisture and stains (especially with a guard coat)
Tire marks and rolling loads
There’s no surface coating to wear through, no film to peel, and no chipping unless the slab itself is damaged.
Grind & Seal: Solid—but Needs Maintenance
Grind & seal finishes can look durable—and to be fair, they’re no slouch in light-use environments. But because they rely on a topical sealer to provide protection, that layer is also the weak point.
Over time, that sealer is going to wear down. In some cases, especially in garages or commercial areas, it can start to dull or peel within 3 to 5 years, depending on traffic and UV exposure.
Here’s where problems start:
Once the sealer breaks down, moisture can get in
Scratches or wear paths show up where people walk most
In sunlit areas, UV can discolor or weaken the coating
Reapplying sealer means shutting down the space again, and it can only be done so many times before a full resurface is needed
For low-traffic residential areas? It might last 7 to 10 years before it needs resealing. But for active households or commercial environments? Expect to redo the sealer every few years to keep it protected and looking fresh.
And in Arkansas?
Arkansas isn’t easy on floors. Between clay-heavy soils, moisture swings, and hot summer sun, you need a system that doesn’t rely on fragile coatings. That’s why we steer clients toward polished concrete for long-term durability—especially in areas that see real use.
Grind & seal is a solid option if you’re okay with the upkeep. But if you want to install it, forget it, and not worry for a couple of decades? Polished concrete is the clear winner.
Maintenance Requirements
When choosing a floor, most people focus on looks and price up front. But what really affects your daily life—and your long-term costs—is maintenance. How much time, money, and effort are you going to spend keeping your floor looking good five years from now?
Here’s how grind & seal and polished concrete stack up in the real world.
Polished Concrete: Practically Self-Sufficient
This is one of the biggest reasons people in Little Rock are moving toward polished concrete—it’s almost effortless to maintain.
Daily and weekly maintenance usually looks like:
Sweeping or dust mopping to remove grit
Damp mopping with a pH-neutral cleaner
Occasionally burnishing or buffing if you want to restore gloss
That’s it. No waxing, no stripping, no sealers to reapply. Because the protection is built into the slab, not sitting on top of it, there’s nothing to wear off.
Even in commercial environments—restaurants, schools, retail stores—we’ve seen polished concrete hold up for years with nothing more than a good cleaning routine. And if it starts to dull? A single pass with a high-speed burnisher brings it right back.
Grind & Seal: Maintenance Comes with the Territory
Grind & seal looks great right after installation. But since the shine and protection come from a film-forming sealer, that layer is going to degrade over time—especially in high-traffic zones, garages, or any space exposed to UV light or moisture.
Here’s what to expect:
Reapply sealer every 2–5 years, depending on traffic and use
Scrub grout lines or joints more frequently in commercial spaces
Touch up scuffs or scratches that break through the sealer
Watch for hazing, dull spots, or bubbling in older coatings
In garages, vehicle tires can cause hot tire pickup—where the sealer lifts under heat and pressure
And keep in mind—each time you reseal, you need to shut down the space, ventilate it properly, and let the coating cure. That adds downtime, especially for businesses.
The Bottom Line on Maintenance
If your goal is a beautiful floor with minimal upkeep, polished concrete wins. It takes less effort, costs less to maintain over time, and holds up without needing frequent refreshes.
Grind & seal isn’t high-maintenance compared to something like carpet or wood, but it does come with a maintenance schedule you can’t ignore—especially if you want it to keep looking its best.
Cost Comparison: What You’ll Actually Spend
Let’s face it—budget matters. Whether you’re renovating a residential space or managing costs on a commercial project in Little Rock, you’ve got to know what you’re walking into. But there’s more to flooring costs than just the number on the quote. It’s about installation, lifespan, and what you’ll be spending five or ten years from now.
Here’s how grind & seal and polished concrete compare when it comes to upfront price and long-term value.
Grind & Seal: The Budget-Friendly Starter
Grind & seal is usually the cheaper upfront option. You’re looking at fewer labor hours, less grinding, and no multi-step polishing process. Materials are lower-cost too—just a sealer, maybe a dye, and some grit if slip resistance is needed.
For homeowners or businesses trying to stretch a tight budget, grind & seal gets the job done. It’s a major visual upgrade from raw concrete and can give you that high-gloss, modern look for a fraction of the cost of polishing.
Where the money goes:
Surface prep and light grinding
Sealer materials and additives
Labor (usually 1–2 days for install)
Optional: tinting/dyes or slip-resistant media
But the catch? It won’t last forever. If you need to reseal every few years—and you factor in labor, materials, and potential downtime—grind & seal can end up costing more than polished concrete in the long run.
Polished Concrete: More Upfront, Less Over Time
Polished concrete takes longer and requires more skill to do right. You’re paying for a multi-step mechanical process, specialized diamond tooling, chemical densifiers, and experienced installers who know how to control the finish.
So yes, the initial price tag is higher than grind & seal. But once it’s done, it’s done. No sealers to reapply. No peeling or touch-ups. No early replacement cycle.
Where your money goes:
Full-depth grinding and leveling
Application of densifier
Multiple rounds of polishing
Optional: color staining, saw cuts, burnishing
And here’s the thing—if you're planning to stay in your home or operate your business in the same location for 10+ years, polished concrete almost always comes out ahead. You pay more once and then coast on maintenance.
Don’t Just Look at the Invoice—Look at the Timeline
Let’s say grind & seal costs less now but needs resealing every 3–5 years. Add in labor, materials, and time lost during reapplication, and that “cheaper” floor becomes an ongoing expense.
Polished concrete? You clean it, maybe burnish it once in a while, and it just keeps performing. That’s real value—especially if you're running a commercial space where downtime is money.
Bottom Line: What Are You Really Buying?
Grind & seal is great when you're on a budget and need a quick win. But polished concrete is an investment in longevity, performance, and peace of mind.
At Rock City Epoxy, we install both—and we’ll tell you straight which one makes more sense for your space and your goals.
Use Cases: Which Is Right for Your Project?
Now that we’ve broken down the technical differences, let’s get practical. Because at the end of the day, this choice isn’t just about features—it’s about fit. What works great in a downtown retail space might be overkill in a guest bedroom. And what holds up in a busy mechanic’s garage might not be necessary for a boutique office.
Here’s how we break it down when helping clients choose between grind & seal and polished concrete—based on real-world Arkansas conditions.
Grind & Seal: Best for Budget-Conscious Projects and Light Use
Grind & seal is a strong option when you're looking for a quick, affordable upgrade that still delivers modern visual appeal. It’s a solid middle-ground between raw concrete and high-end finishes.
Great for:
Residential garages or basements where wear-and-tear is minimal
Retail spaces with modest foot traffic and tight timelines
Restaurants and breweries looking for a gritty, industrial aesthetic
Short-term or temporary commercial spaces
Flipping or selling a property where appearance matters more than long-term durability
It’s also a smart choice when you need something that looks sharp for lower upfront cost, especially if you’re okay with resealing it every few years.
But—be honest with yourself. If you expect heavy use, lots of foot traffic, water, UV, or rolling loads, you’re going to fight against the limits of a surface sealer.
Polished Concrete: Best for Long-Term Performance and High Use
Polished concrete isn’t just about style—it’s a high-performance system that’s built for the long haul. We recommend it for any project where durability, ease of maintenance, and visual impact are high priorities.
Ideal for:
Commercial offices and high-traffic retail spaces
Restaurants, bars, and cafes with constant foot traffic
Modern homes with open-concept layouts
Warehouses, factories, and industrial shops
Schools, government buildings, and healthcare facilities
Any space where moisture or Arkansas humidity is a factor
If your goal is to install it once and not worry for 15+ years, polished concrete is the way to go. It's especially well-suited to Little Rock’s clay-heavy soils and seasonal humidity, where coatings like sealers tend to break down faster.
Still Not Sure? Here’s the Gut Check
Ask yourself:
Is this space low-traffic or high-traffic?
Do I want a budget finish or a long-term investment?
Will I be okay resealing this floor in 3–5 years?
Do I need maximum durability, or is this more for looks?
Am I building this space for 5 years or 20?
Once you answer those questions, the right system usually becomes clear.
Final Recommendation from Rock City Epoxy
At this point, you’ve seen both sides. Grind & seal and polished concrete can both deliver clean, modern floors—but they’re built for very different situations. One isn’t “better” across the board. It comes down to what you need from your floor, and how long you expect it to perform.
Here’s our no-nonsense take:
If you’re on a tighter budget, working with a short-term lease, or just need something that looks good fast—grind & seal is a great fit. It gives you a sleek appearance, quick turnaround, and a much-needed upgrade from raw concrete. Just go into it knowing you’ll be resealing and maintaining it more often, especially in active spaces.
But if you’re building a long-term space—your home, a business you plan to grow, or a commercial facility where downtime costs money—go with polished concrete. Yes, it costs more upfront. But it’s also tougher, easier to live with, and built to last for decades.
Polished concrete isn’t for everyone. But for the right space, it’s the last floor you’ll ever need.
At Rock City Epoxy, we install both systems—and we’re not here to upsell you. We’re here to help you make the right decision for your space, your goals, and your budget. If you’ve got questions, bring them. If you want honest answers, you’ll get them.
Let’s Talk About Your Project
Not sure which floor system is right for you? That’s exactly what we’re here for.
At Rock City Epoxy, we don’t do cookie-cutter solutions. We do real floors for real people—homeowners who want something clean and low-maintenance, and business owners who need performance without the hassle. Whether you’re leaning toward polished concrete or considering grind & seal for your space, we’ll give you a straight answer and a plan that fits your goals.
You’ll talk directly with TJ—no sales reps, no pressure.
Want a free quote or just want to run some ideas past us? You’ve got three easy ways to reach out:
Call or Text: (501) 408-6160
Email: [email protected]
Contact Form: Fill out the short form on our website and we’ll follow up ASAP with answers, pricing, and next steps
We serve Little Rock and surrounding areas—including North Little Rock, Sherwood, Conway, Benton, Maumelle, Bryant, and beyond.
Let’s make your concrete floor the kind of upgrade you don’t have to second guess.