
Battle of the Floors: Should You Choose Epoxy or Polished Concrete?
Why the Right Concrete Floor Choice Matters
When it comes to upgrading the floors in your home or business, not all concrete systems are created equal—and picking the wrong one can cost you more than just money. In Little Rock and the surrounding areas, we see it all the time: floors that looked great for the first year, only to crack, stain, peel, or wear down under real-world use.
That’s why choosing between epoxy flooring and polished concrete isn’t just a design decision—it’s a business decision. It’s about how you want your floor to perform when the Arkansas humidity kicks in, when the trucks start rolling over it, or when foot traffic never seems to stop.
At Rock City Epoxy, we specialize in helping property owners make the right call. Whether you’re restoring a commercial showroom, resurfacing a shop floor in Benton, or giving your Little Rock garage the upgrade it deserves, knowing the difference between epoxy coatings and polished concrete could save you thousands down the line—and give you a surface that works as hard as you do.
In this guide, we’re diving deep into the battle of the floors: epoxy versus polished concrete. We’ll break down how each system holds up in the real world, what you can expect in terms of cost, maintenance, and longevity, and how to decide which is the right investment for your specific space. No fluff, no confusing jargon—just real answers from experts who install both every day across Central Arkansas.
1. What Is Epoxy Flooring? (And Why It’s Not Just 'Paint')
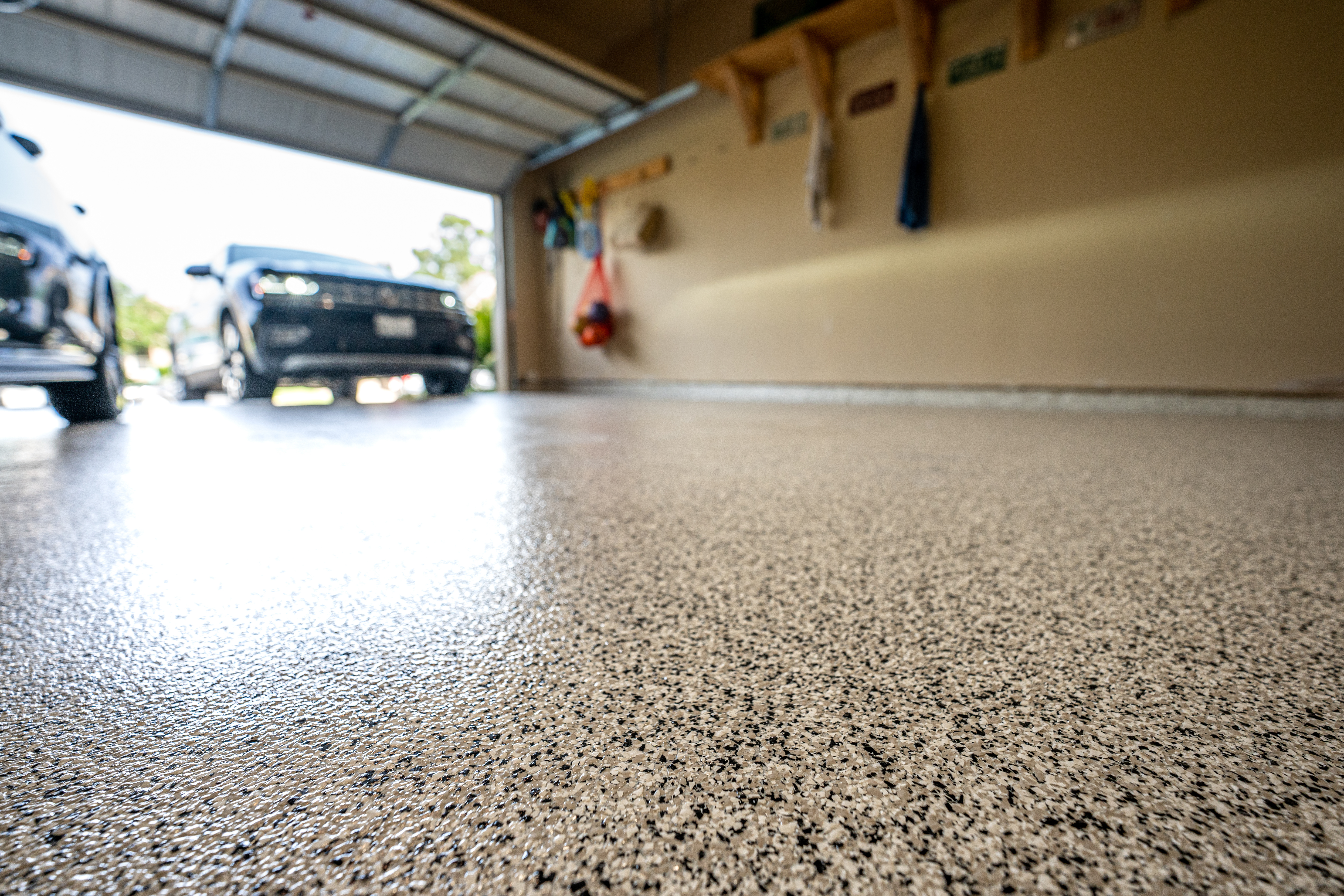
If you’ve heard someone say, “Yeah, epoxy’s just fancy paint,” do yourself a favor and smile—then walk away.
Because real epoxy flooring is on a whole different level.
Epoxy flooring is a high-performance, industrial-grade coating system made by mixing two separate components: a resin and a hardener. When combined, they chemically react to create a bond that's stronger than either material on its own. We’re talking about a surface that doesn't just sit on top of your concrete slab—it becomes part of it.
At Rock City Epoxy, we only install true 2-part epoxy systems—no shortcuts, no hardware store DIY kits pretending to be professional-grade. A proper epoxy floor, like the ones we install across Little Rock, Benton, Bryant, and surrounding areas, is designed to:
Resist heavy impacts from tools, vehicles, and machinery.
Stand up to chemicals like oils, solvents, and cleaning agents.
Create a seamless surface that's easy to clean and sanitize.
Enhance slip resistance with broadcast additives when needed.
Deliver custom looks—from solid colors to metallic swirls to industrial quartz blends.
The secret sauce isn’t just in the materials—it’s in the prep work.
Before epoxy is applied, we mechanically grind the surface using diamond grinders to open up the concrete’s pores and remove any weak or contaminated material. This step ensures the epoxy actually bonds into the surface—not just onto it—giving you a floor that lasts for decades, not months.
Pro Insight:
When installed correctly, a 100%-solids epoxy floor in a busy commercial garage in Little Rock can easily hold up for 20+ years with basic maintenance. Compare that to a budget coating or a roll-on "epoxy paint," which might start peeling before the Razorbacks’ next football season even kicks off.
In other words, epoxy flooring isn’t just about making concrete look better—it’s about engineering a protective armor for your slab.
And it’s not a one-size-fits-all deal either. Different spaces call for different types of epoxy systems:
High-build epoxy for industrial warehouses
Decorative flake epoxy for garages and basements
Metallic epoxy for showrooms and modern interiors
Each system is custom-designed based on how the floor will actually be used—not some cookie-cutter install. That’s why Rock City Epoxy floors work—they’re built specifically for the conditions they're going to face, not just for how they’ll look on day one.
Next up, let's flip the script and look at the other contender in this flooring battle: polished concrete.
2. What Is Polished Concrete? (And How It’s Totally Different)
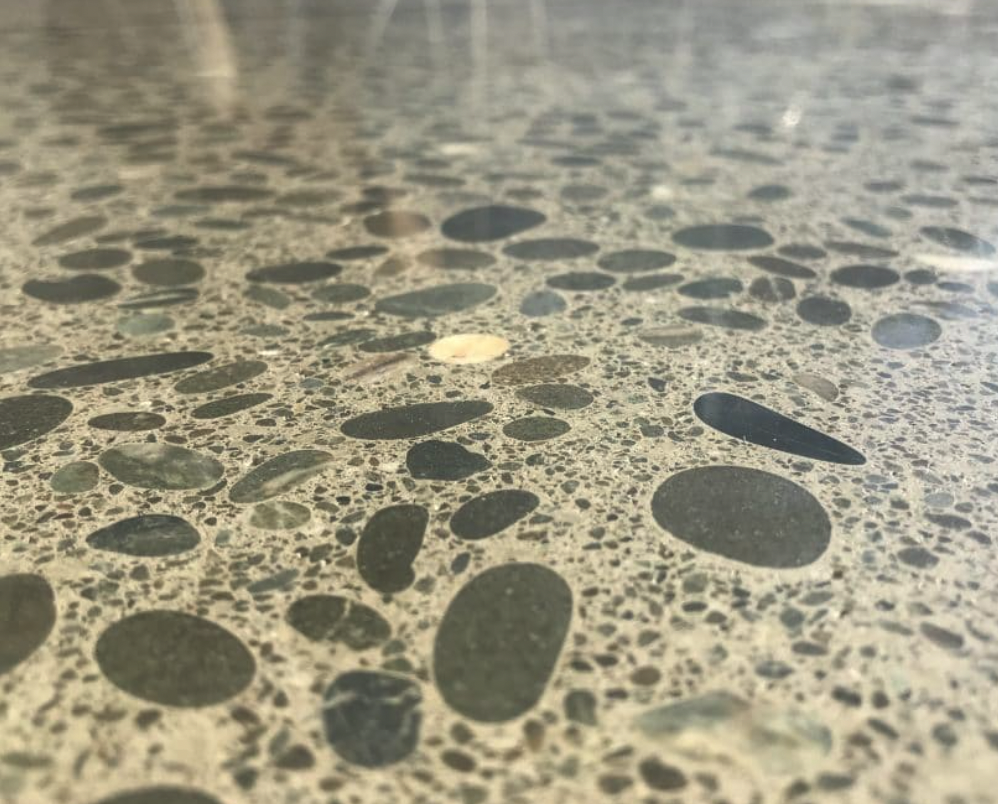
Now, if epoxy is about adding a protective armor over your slab, polished concrete is about transforming the slab itself into the star of the show.
Polished concrete isn’t a coating. It’s not something you pour over the surface. It’s a mechanical process that takes your existing concrete and, through a series of heavy grinding and honing steps, refines it into a dense, durable, and highly reflective floor. Think of it like taking a rough piece of wood and sanding it down until it’s smooth as glass—only this time, it’s your concrete slab getting the high-end treatment.
At Rock City Epoxy, when we polish concrete floors across Little Rock, Bryant, and North Little Rock, we don’t cut corners. We use industrial-grade grinders and progressively finer diamond tooling to open up the surface, remove imperfections, and create a consistent finish. Then, we apply densifiers—special chemical hardeners that penetrate deep into the concrete and strengthen it from the inside out.
Here’s what polished concrete delivers when it’s done right:
Incredible durability without needing a separate coating.
A beautiful natural look, from satin to high-gloss finishes.
Low maintenance—no waxing, no sealing every year.
Better light reflection, which can reduce lighting costs in warehouses and showrooms.
Stain resistance once properly densified and polished.
Pro Insight:
When properly installed, a polished concrete floor inside a Little Rock retail store can handle tens of thousands of footsteps per day with barely any visible wear. In fact, many major big-box retailers (you know the ones) use polished concrete because it’s cost-effective, tough as nails, and easy to maintain over the long haul.
But here’s the reality check:
Polished concrete isn’t a magic bullet.
It won’t hide cracks, pits, or deep stains—your slab’s existing condition shows through.
It’s not naturally chemical resistant the way epoxy is.
And while polished concrete is hard, it’s still porous—if not properly densified and maintained, it can absorb oils, spills, and salts over time.
That’s why polishing is a great choice for clean, heavy-traffic interiors, but not always ideal for places like auto shops, kitchens, or garages where chemical exposure, staining, and wet conditions are the norm.
At the end of the day, polished concrete is about bringing out the strength and character of the concrete you already have, not covering it up or hiding its flaws.
So now that you know what both systems are really about, it’s time to get serious:
How do epoxy and polished concrete stack up when they go head-to-head?
3. Head-to-Head Comparison: Performance Factors That Matter
Choosing between epoxy flooring and polished concrete isn’t just about picking a color or chasing a trend—it’s about performance. When you're investing serious money into your floors in Little Rock, Benton, or Bryant, you need to know exactly how each option stacks up where it counts.
Let’s get into the real-world factors that should drive your decision.
Durability
If you're building out a space that’s going to take a beating—think tool drops, forklift traffic, chemical spills—epoxy flooring is the tank you want.
Properly installed, a 100%-solids epoxy system creates a hard, flexible surface that absorbs impact and resists abrasion.
Polished concrete? It's tough too, but it’s still, at the end of the day, concrete. It can chip, crack, or pit under repeated heavy impacts, especially if the original slab has flaws or isn’t thick enough to handle industrial use.
Bottom Line:
Heavy use, chemical exposure, mechanical wear? Epoxy wins hands down.
Light to medium foot traffic in a clean environment? Polished concrete holds up great.
Aesthetics
Both epoxy and polished concrete can look amazing—but they’re different beasts when it comes to style.
With epoxy flooring, the design options are practically endless:
Solid colors to match branding or décor.
Metallic finishes that create high-end showroom floors.
Decorative flakes that add texture and hide imperfections.
Quartz or broadcast floors for serious industrial style and slip resistance.
Meanwhile, polished concrete offers a sleek, natural look. The final appearance depends heavily on the quality of your original slab—aggregate exposure, color variations, and imperfections are all part of the final result. You can choose levels of sheen, from satin to mirror-like gloss, but you’re working with the character of the concrete itself.
Bottom Line:
Want full creative control over color, texture, and design? Go epoxy.
Love the clean, natural beauty of concrete itself? Polished concrete is your move.
Maintenance
One of the biggest selling points for both systems is ease of maintenance—but again, there’s a difference in expectations.
Epoxy flooring is seamless, non-porous, and highly resistant to most chemicals. Cleaning is usually as simple as a mop, a soft scrubber, and some gentle degreaser. Over time (especially in commercial spaces), you may need to reapply a clear topcoat every 5–7 years to keep that “like-new” shine and protection.
Polished concrete is very low maintenance too. Regular dry dust mopping and occasional wet mopping are usually enough. But polished concrete can lose its luster over time, especially in high-traffic areas. Every few years, a re-burnish or light re-polish might be needed to maintain its appearance.
Bottom Line:
Epoxy needs periodic re-topcoating to stay at peak performance.
Polished concrete may need periodic re-burnishing to maintain gloss.
Neither is totally maintenance-free—nothing truly is—but both are great options compared to tile, VCT, or bare concrete.
Slip Resistance
Both epoxy and polished concrete can be made slip-resistant, but how they do it—and how well it works—differs.
With epoxy flooring, we can broadcast additives like silica sand, polymer grit, or aluminum oxide right into the topcoat. This gives us precise control over the texture and traction based on your needs—whether it’s light grip for residential garages or aggressive non-slip for commercial kitchens.
Polished concrete, on the other hand, gets slip resistance from its surface profile. Higher-grit finishes tend to be slicker, while lower-grit finishes offer more traction. However, wet polished concrete can still get slippery if not properly treated with traction-enhancing conditioners or finishes.
Bottom Line:
Need customized slip-resistance? Epoxy gives you more control.
Want a basic level of slip-resistance with a smooth finish? Polished concrete can deliver, but with less fine-tuning.
Installation Time and Cost
Here’s where the choice gets real, especially for businesses in Little Rock that can’t afford to be shut down for long.
Polished concrete tends to be faster to install if your slab is in good condition. Minor repairs, grinding, densifying, polishing—it’s a few days’ work depending on size. It's also usually cheaper upfront because you're not adding materials—you're working with the concrete itself.
Epoxy flooring, especially multi-layer systems like flake or metallics, can take longer. Surface prep (grinding or shot blasting), primer, basecoat, broadcast, and topcoat—all need proper cure times between stages. It’s a more material-intensive process and can cost more initially, but you’re getting a whole new engineered surface, not just a finish.
Bottom Line:
Budget-conscious with a solid existing slab? Polished concrete could save you upfront.
Need maximum protection and durability? Epoxy is worth the extra investment.
Longevity and ROI
If installed correctly and maintained properly, both systems offer excellent longevity—but they excel in different ways.
A properly installed epoxy floor can last 20+ years even under heavy traffic, and because it forms a protective shield, it prevents costly slab repairs underneath. You get a serious return on investment if you’re protecting a valuable workspace, auto shop, or industrial facility.
Polished concrete can last just as long if it’s not subjected to chemical attack, heavy gouging, or oil saturation. It’s a great long-term option for retail, warehouse, and residential spaces where protection from chemicals isn’t as critical.
Bottom Line:
Commercial/industrial settings where abuse is high? Epoxy wins for ROI.
Large clean spaces where budget matters? Polished concrete stretches your dollar further.
The Verdict: No One-Size-Fits-All Winner
Here’s the real deal: it’s not about which floor is better—it’s about which floor is better for you.
If you need toughness, chemical resistance, design flexibility, and you’re protecting valuable operations or inventory, epoxy flooring is going to give you a better return on investment in Little Rock's tough, humid climate.
If you need clean aesthetics, high durability under foot traffic, and lower initial cost for a large space, polished concrete could be the smart play.
4. Best Applications for Epoxy Flooring
Epoxy flooring isn’t a trend—it’s a strategic move. When durability, safety, and design flexibility matter, epoxy doesn’t just step up... it takes over.
Here’s where epoxy flooring really shines in Little Rock, Benton, Bryant, and across Central Arkansas:
Garages and Workshops
If you’re parking trucks, storing tools, or doing any serious mechanical work, garage epoxy systems are a no-brainer.
Oil spills? No problem.
Dropped tools? Barely a scratch.
Tire marks? They wipe right off.
In residential garages across Little Rock, our flake epoxy floors add not just toughness, but style—turning dull slabs into clean, professional-looking spaces that stay easier to maintain year after year.
Commercial Showrooms
Auto dealerships, retail stores, furniture outlets—you name it. These places need floors that can handle heavy foot traffic, rolling displays, and still look sharp at the end of the day.
With options like metallic epoxy or custom-colored designs, we can match your brand colors, add logos, or create high-gloss finishes that leave a serious first impression.
Warehouses and Distribution Centers
In commercial and industrial settings, durability isn’t optional—it’s mandatory.
An industrial epoxy system with quartz broadcast or heavy-duty topcoats protects your concrete against:
Constant forklift traffic
Dragging pallets
Chemical spills
Hard impacts
Plus, epoxy’s seamless finish makes cleaning up Arkansas’s red clay dust a whole lot easier.
Restaurants and Commercial Kitchens
Slip-resistant, easy to sanitize, and tough enough to stand up to heavy equipment and food service demands—epoxy flooring checks all the boxes for commercial kitchens in Little Rock and the surrounding areas.
We can also install coving (curved epoxy bases) along walls for even easier cleanup and better health code compliance.
Medical Facilities and Laboratories
In environments where cleanliness and chemical resistance are non-negotiable, epoxy delivers.
Seamless surfaces mean no grout lines or cracks where bacteria can hide, making it a natural fit for hospitals, clinics, labs, and research facilities.
Retail Spaces and Offices
For modern, low-maintenance, stylish floors that turn heads, many retail owners and office managers are leaning into decorative epoxy floors.
Metallic finishes, colored quartz, and custom flake blends let you create spaces that feel polished without the constant upkeep of carpet or tile.
Pro Insight:
In Little Rock's humid climate, epoxy’s non-porous nature protects floors from moisture vapor damage—a hidden but real threat to untreated or poorly protected slabs.
Bottom line:
If you need a floor that protects, performs, and impresses—epoxy should be at the top of your list.
But what about polished concrete? Let’s flip the page and talk about where it dominates.
5. Best Applications for Polished Concrete
When it comes to combining natural beauty, low maintenance, and long-term durability, polished concrete brings some serious muscle to the table.
It’s not the right fit for every project, but when it’s used correctly, it absolutely delivers.
Here’s where polished concrete really flexes across Little Rock, Benton, Bryant, and beyond:
Large Retail Spaces
Think big-box stores, grocery chains, and outlet malls.
Why do so many national retailers rely on polished concrete? Simple:
It’s tough enough to survive thousands of footsteps, shopping carts, and rolling displays.
It reflects light, making stores brighter without additional electricity costs.
It stays looking clean without the constant need for waxing or sealing.
In large commercial spaces around Little Rock, polished concrete floors stretch budgets further without sacrificing aesthetics.
Industrial Warehouses and Distribution Centers
If your operation is mainly foot traffic and forklift movement without heavy chemical exposure, polished concrete is an efficient, cost-effective flooring choice.
Densified and polished surfaces resist abrasion and dusting, which means:
Less maintenance downtime.
Cleaner air quality inside the facility.
Longer slab life without needing coatings or coverings.
Pro Insight:
Many facilities around Little Rock use polished concrete because it minimizes particulate dust—a real problem in unsealed or untreated warehouses.
Office Buildings and Corporate Interiors
More companies are ditching carpet tiles and laminates in favor of polished concrete for one simple reason: It looks sharp without the maintenance headache.
With the right grind and polish levels, you can achieve anything from a soft, satin-like surface to a mirror finish. Add some tasteful scored patterns or subtle stains, and you get a floor that’s modern, clean, and impressively durable.
Schools, Universities, and Public Facilities
Polished concrete makes a ton of sense for educational and public spaces across Arkansas:
It’s safe and slip-resistant.
It lowers long-term maintenance costs dramatically.
It handles everything from muddy boots to rolling backpacks without missing a beat.
High-traffic areas like hallways, cafeterias, and gym entrances thrive with polished concrete.
Residential Interiors and Modern Homes
Minimalist home design is booming—and polished concrete fits the style perfectly.
Inside homes in Little Rock and the surrounding areas, polished concrete delivers:
Cool, industrial-modern looks.
Easy-clean living (especially great for allergy sufferers).
Thermal mass benefits for energy efficiency in our hot Arkansas summers.
You’ll often see polished concrete in living rooms, kitchens, and even outdoor patios where homeowners want something sleek but extremely durable.
Museums, Galleries, and Event Spaces
For spaces where looks and function matter, polished concrete strikes the right balance.
In museums and art galleries, the natural, understated finish of polished concrete lets exhibits stand out. Meanwhile, the hard-wearing surface quietly handles crowds without constant repairs or upkeep.
Bottom line:
If you have a large, clean-space project that needs toughness, style, and cost-efficiency, polished concrete should absolutely be in the conversation.
But like any system, it isn’t perfect everywhere.
That’s why the next thing we need to bust through are the common myths about both floors—because when people make bad flooring choices, it's usually because they fell for bad information.
6. Common Misconceptions About Epoxy and Polished Concrete
When people start researching flooring options, they run into a wall of half-truths, old-school myths, and flat-out bad advice.
Let’s clear the air and set the record straight—because making the wrong decision based on bad information can cost serious money down the road.
Here are the most common myths we hear around Little Rock—and what you really need to know:
"Epoxy Peels Easily"
This one gets thrown around a lot by people who’ve seen cheap DIY epoxy kits fail—or worse, had a contractor skip proper surface prep.
Here’s the truth:
Epoxy flooring only peels when it's installed improperly.
If the slab isn’t mechanically ground to open the pores, or if there’s moisture vapor coming up from below and it isn’t addressed, then you get failure.
But when installed the right way—like we do at Rock City Epoxy—epoxy floors bond permanently to the concrete, creating a chemical connection that’s stronger than the slab itself.
Pro Insight:
A professionally installed 100%-solids epoxy floor in a Little Rock commercial garage can easily outlast the vehicles parked on it.
"Polished Concrete Doesn’t Need Maintenance"
It’s true that polished concrete is low-maintenance—but low maintenance doesn't mean no maintenance.
Polished floors still need:
Regular dust mopping to remove grit that can scratch the surface.
Occasional wet mopping with a pH-neutral cleaner.
Periodic re-burnishing or re-polishing, especially in high-traffic zones.
Skip the basic care, and your polished concrete can start to look dull, stained, and worn a lot faster than you think.
"Epoxy Looks Cheap"
Sure—if it’s done badly.
A slapped-on DIY kit with no broadcast media, no primer, and one thin layer will absolutely look cheap.
But professional epoxy systems? Different world.
Metallic epoxies create deep, 3D effects that look like luxury stone.
Flake floors create vibrant, textured finishes that hide dirt and wear beautifully.
Solid color epoxies deliver clean, high-gloss floors that elevate garages, shops, and showrooms.
In short:
Epoxy can look industrial, artistic, sleek, or rugged—depending on how you design it.
"Polished Concrete Hides All Flaws"
Unfortunately, polished concrete is like a magnifying glass for your slab’s imperfections.
If your concrete has:
Cracks
Stains
Uneven patches
Poor pours or rough finish work
...those flaws will still be visible after polishing. Sometimes you can work them into the "character" of the floor (especially in rustic designs), but polishing doesn’t erase history—it highlights it.
"Epoxy and Polished Concrete Are Basically the Same"
Nope. Not even close.
Epoxy is a surface system engineered to protect the concrete underneath.
Polished concrete is the concrete itself, mechanically hardened and refined into a finished surface.
Different materials.
Different installation processes.
Different strengths and weaknesses.
Choosing between them without understanding the difference is like choosing between a pickup truck and a motorcycle—they’re both vehicles, but they’re built for completely different jobs.
Bottom line:
When you get past the myths, you can make a flooring decision that actually fits your space, your budget, and your future plans—not just what sounds good online.
Speaking of future plans...
If you’re in Little Rock or anywhere around Central Arkansas, there’s something else you need to think about before you pull the trigger: local factors.
Because not every floor system handles Arkansas the same way.
7. Little Rock Factors to Consider Before Choosing Your Floor
If every concrete slab were the same, picking the right floor system would be easy.
But in Little Rock and across Central Arkansas, local conditions play a massive role in what’s going to hold up—and what’s going to fail fast.
Before you decide between epoxy flooring and polished concrete, here’s what you need to factor in:
Arkansas Humidity and Moisture Vapor
Let’s be real—our summers in Little Rock get brutally humid.
That humidity doesn’t just sit in the air. It tries to rise up through concrete slabs, especially in garages, basements, and ground-level commercial spaces.
If that moisture vapor isn’t handled correctly, it can wreck a flooring system before it ever has a chance.
Epoxy flooring requires a moisture-tolerant primer if the slab isn’t properly vapor-sealed. Otherwise, pressure from underneath can cause blistering or delamination.
Polished concrete breathes a little more naturally, but it’s still vulnerable. Moisture can carry minerals to the surface, causing efflorescence (those ugly white stains) if densification and polishing aren't dialed in right.
Pro Insight:
At Rock City Epoxy, we always test slabs for moisture vapor emissions before installing a floor—because guessing is how projects fail.
Freeze-Thaw Cycles
Little Rock winters might not be the worst, but we do get freeze-thaw cycles.
When water inside concrete freezes, it expands, putting stress on the slab.
Exterior polished concrete (like patios or driveways) can spall or crack without proper sealing and maintenance.
Epoxy floors indoors don’t typically see direct freeze-thaw action, but garages and shops without climate control can experience problems if moisture isn’t addressed early.
Choosing the right floor prep, primers, and topcoats matters even more in spaces that see big temperature swings.
Traffic Load and Usage Type
Not all traffic is created equal.
A downtown Little Rock restaurant gets foot traffic and food spills.
A Benton warehouse gets forklifts and pallet drags.
A residential garage in Bryant gets tires, tool drops, and maybe a few muddy boots.
Each situation demands a different kind of toughness:
Heavy chemical exposure or mechanical abuse? Go epoxy.
High-volume clean foot traffic with minimal chemicals? Polished concrete can shine.
Matching the floor to the usage isn’t optional—it’s the difference between an investment and a liability.
Existing Slab Condition
Another huge factor: what kind of concrete are we working with?
If the slab is old, cracked, stained, or uneven, polished concrete may not be the best look—it’ll highlight every flaw.
If the slab is in decent shape but needs protection, epoxy can not only cover minor imperfections but add layers of defense.
In Little Rock’s older homes and commercial buildings, slab condition varies wildly.
That’s why we always recommend a site visit and a real evaluation before quoting anything.
Aesthetic Goals and Branding
Finally, let's not forget: how your floor looks matters.
If you’re running a commercial space where first impressions count—like a showroom, a gym, or a boutique—then design flexibility is a major factor:
Want custom colors, logos, high-gloss, or metallic effects? Epoxy wins easily.
Want a clean, minimalist, natural concrete look? Polished concrete is your answer.
Both can look stunning when done right—it just depends on the vibe you're trying to create.
Bottom line:
There’s no “one size fits all” answer for flooring in Little Rock.
You have to think about moisture, traffic, climate, slab condition, and aesthetics—and then pick the system that's going to work with the environment, not against it.
And the good news?
You don’t have to figure it out alone.
At Rock City Epoxy, we’ve been helping homeowners, business owners, and facility managers across Little Rock, Benton, Bryant, and Central Arkansas make smart flooring choices that stand the test of time.
8. How Rock City Epoxy Delivers the Best of Both Worlds
Picking between epoxy flooring and polished concrete isn’t just about materials—it’s about having the right team behind the installation.
Because even the best product will fail if it’s installed poorly or matched to the wrong environment.
At Rock City Epoxy, we don’t just sell floors—we build systems that are customized for how you actually use your space.
Whether you’re a homeowner looking to upgrade a garage in Bryant, a business owner building out a showroom in Little Rock, or a facility manager overseeing a distribution center in Benton, we bring the experience, craftsmanship, and real-world knowledge you need to get it done right the first time.
Epoxy Flooring Experts
When it comes to epoxy, cutting corners isn’t an option.
That’s why Rock City Epoxy installs true 100%-solids epoxy systems, backed by:
Mechanical surface preparation (diamond grinding or shot blasting)
Moisture mitigation testing and treatment (critical in Little Rock’s climate)
Customizable finishes (flakes, metallics, quartz, solids—designed for how you use the space)
Heavy-duty topcoats for chemical resistance, slip protection, and long-term durability
Every epoxy floor we install is built for the real-world demands it’s going to face—not just what looks good on install day.
Polished Concrete Professionals
When polishing concrete, it’s the small details that separate amateurs from pros.
At Rock City Epoxy, we use:
Industrial-grade grinders with progressively finer diamond tooling
Concrete densifiers that actually penetrate and strengthen the slab—not just coat it
Precision polishing techniques that create beautiful, consistent finishes without shortcuts
Careful slab evaluation to set realistic expectations and deliver the best possible result
Whether you want a soft satin sheen for a residential living space or a high-gloss mirror finish for a retail store, we know how to customize the polish for your needs.
Why Rock City Epoxy?
Because we treat every project like it’s our own shop, garage, or business.
Real prep work—not just surface scratching
Right system for the right space—not a one-size-fits-all package
Clear communication and no surprise pricing
Local experts who actually understand what Arkansas concrete and Arkansas weather do over time
From Little Rock to Benton to Bryant and all across Central Arkansas, we’re known for floors that not only look amazing but actually last.
Whether it’s an industrial-strength epoxy system for your shop, a decorative flake garage floor, or a polished concrete surface for a brand-new retail space, Rock City Epoxy is the team that delivers floors built for real life—not just showroom photos.
And we’re ready to help you find the perfect solution for your space.
Find the Right Floor for Your Space with Rock City Epoxy
When it comes to protecting your investment, your business, or your home, the floor you choose matters more than most people realize.
Both epoxy flooring and polished concrete offer incredible advantages—but only when they’re installed correctly and matched to the real-world demands of your space.
And here in Little Rock and across Central Arkansas, not every slab—and not every environment—is created equal.
At Rock City Epoxy, we don’t just throw down a product and hope it sticks. We take the time to understand how you use your space, what your concrete needs to perform long-term, and which system—epoxy or polished concrete—is going to deliver the best value, durability, and look for years to come.
Because a great floor isn’t just about today.
It’s about tomorrow, and every day after.
Ready to build a floor that works as hard as you do?
Give TJ at Rock City Epoxy a call at 501-408-6160 or shoot us an email at [email protected]
Let's talk about the space you’re building—and how we can help you make it stronger, better, and built to last.