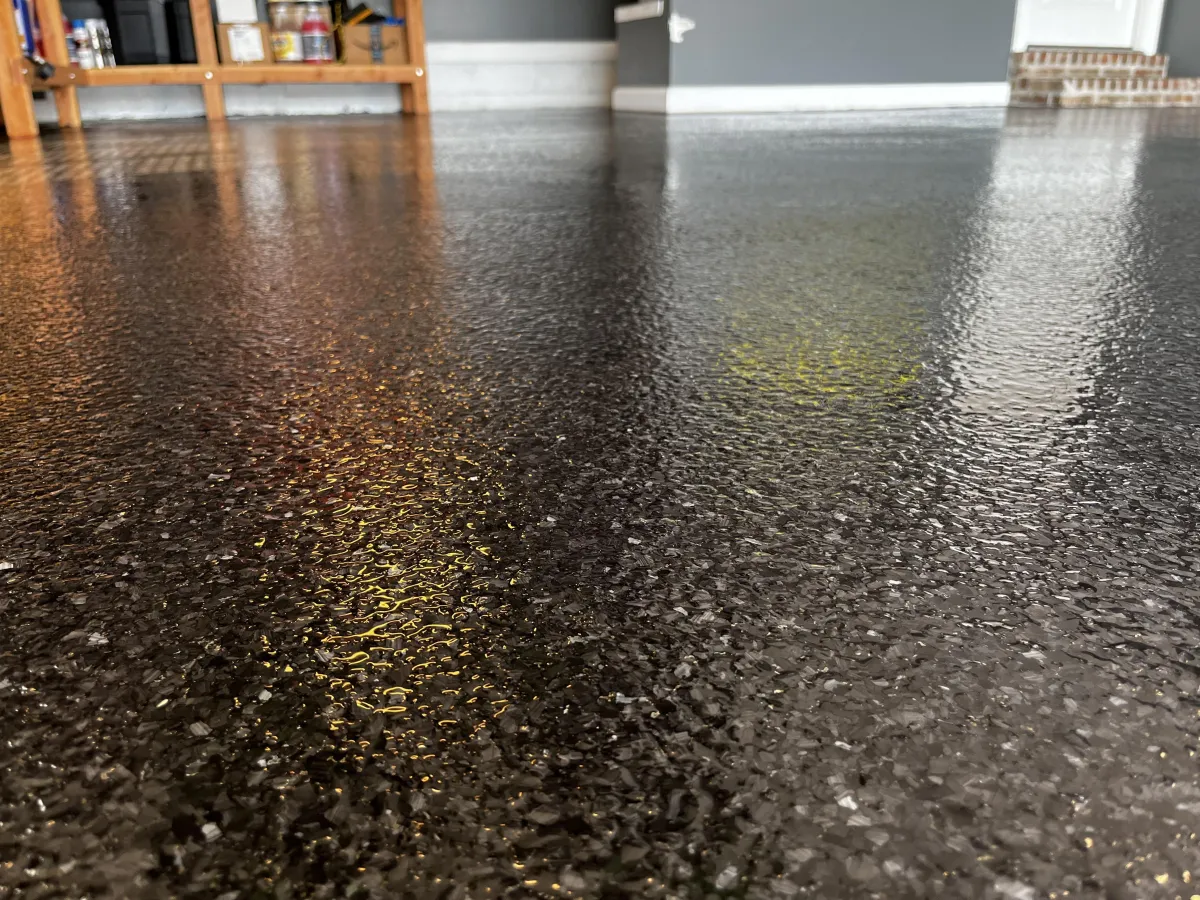
2-Part Epoxy vs. Epoxy Paint: Garage Floor Guide Little Rock
The Garage Floor Mistake People Don’t Know They’re Making
Let’s cut through the noise—most homeowners walking into a big-box store think they’re buying “epoxy” when they grab a can labeled epoxy paint. Sounds legit, right? It says “epoxy,” it promises durability, and it costs way less than hiring a pro. But here’s the thing: not all epoxy is created equal, and choosing the wrong product for your garage floor can lead to peeling, staining, hot tire pickup, and a whole lot of wasted money.
At Rock City Epoxy, we’ve seen it all—failing DIY jobs done just a year ago, “epoxy” floors that can’t handle a parked car, and homeowners frustrated because what was supposed to be a weekend win turned into a costly do-over. The root cause? Confusion between true 2-part epoxy coatings and low-grade 1-part epoxy paint.
This blog is your no-nonsense guide to understanding the difference. We’ll walk you through what each product really is, how they perform under real-world garage conditions here in Little Rock, and why going with a pro-grade solution could save you thousands in the long run. If you’ve been staring at your bare concrete wondering what your next move should be—start here. We’re breaking it all down so you don’t waste time, money, or your next free weekend.
What Is “Epoxy Paint”?
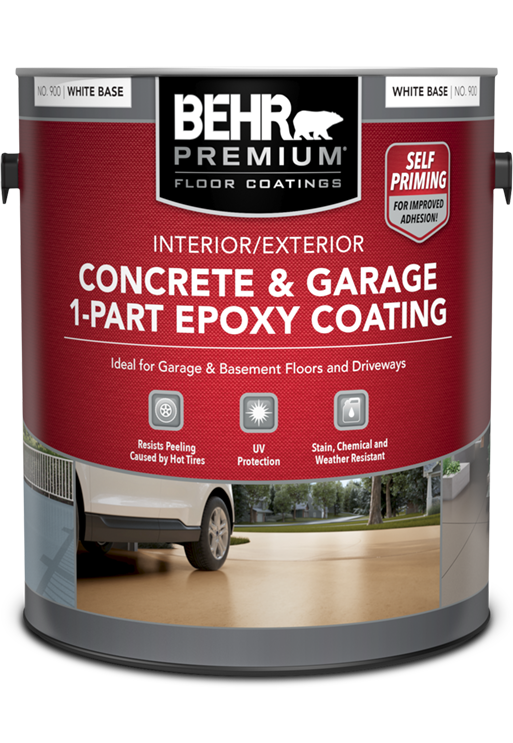
Here’s the hard truth: most of what’s sold in hardware stores as “epoxy” isn’t the real deal. That gallon you picked up at Home Depot? It’s usually 1-part epoxy paint—a glorified latex or acrylic paint with just enough epoxy resin blended in so it can legally use the word “epoxy” on the label. But make no mistake, this is paint with marketing, not a professional-grade flooring system.
The chemistry is what gives it away. True epoxy coatings come in two parts: a resin and a hardener. Mix them together, and you kick off a chemical reaction that bonds the coating to the concrete—creating a hard, durable surface that resists chemicals, hot tires, and heavy loads. But 1-part epoxy paint doesn’t work that way. It dries through evaporation, just like standard wall paint. There's no chemical bonding, no deep penetration into the concrete, and no industrial-grade protection.
Manufacturers position these products as DIY-friendly. They go on easy with a roller, don’t require fancy equipment, and dry in a few hours. But what they don’t mention is what happens after the install. We’re talking early peeling, fading under UV light, soft spots from hot tires, and zero defense against the oil, grease, and road salts that get tracked into your garage.
And while they might look great for the first few weeks, epoxy paints are notorious for yellowing, chalking, and losing their shine—especially in garages that get a lot of sunlight and temperature swings, like we see here in Little Rock.
To be clear, epoxy paint isn’t useless. It can work in very light-duty indoor spaces, like laundry rooms or storage closets. But if you’re parking vehicles, running tools, or just want something that lasts more than a year or two, 1-part paint is not the coating you want on your garage floor.
What Is True 2-Part Epoxy?
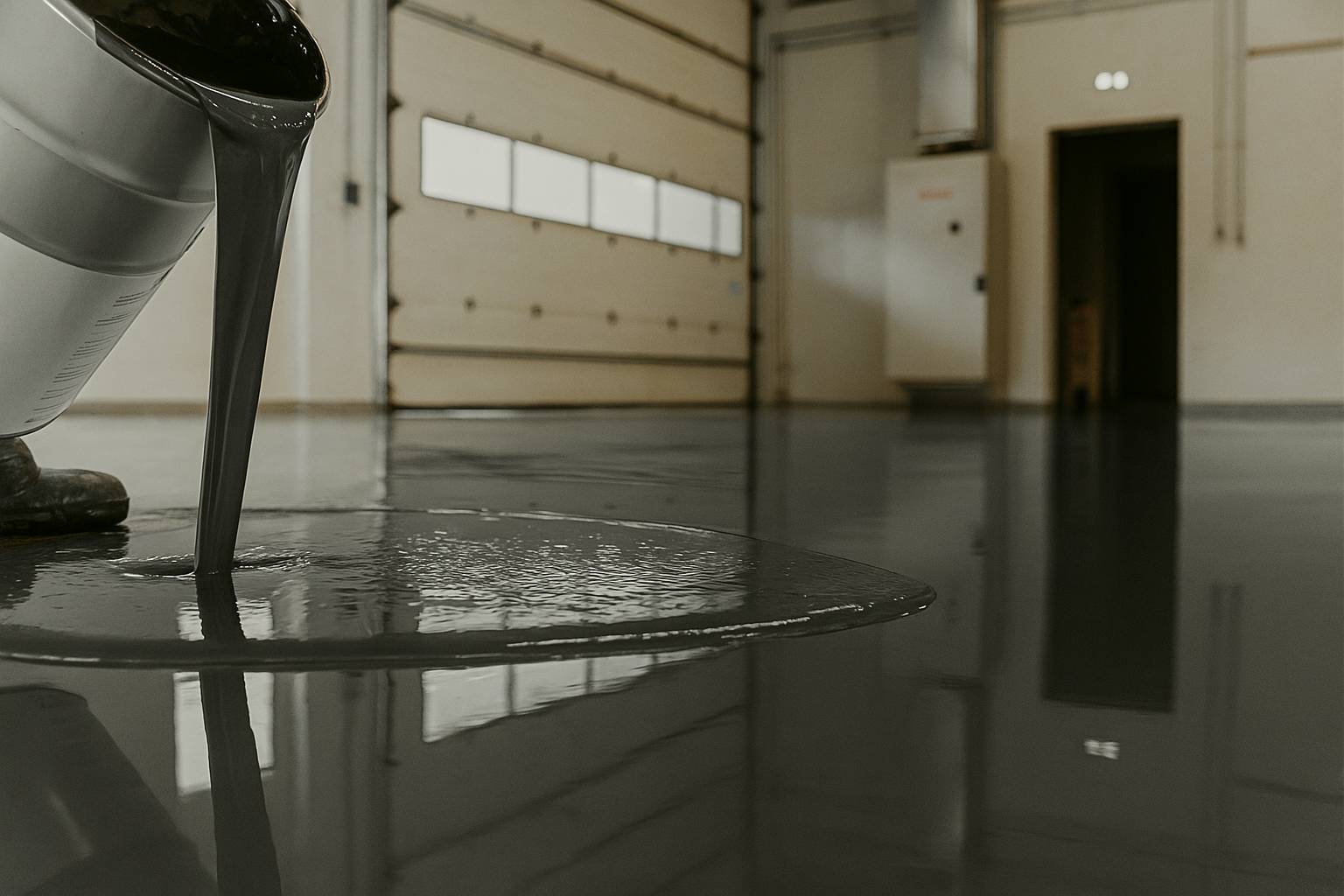
If 1-part epoxy paint is just dressed-up latex, then true 2-part epoxy is the real muscle under the hood. This is the system pros like Rock City Epoxy use every day for garage floors that take a beating and still look showroom-ready for years. It’s not a gimmick. It’s chemistry.
Here’s how it works: 2-part epoxy systems come in two separate containers—Part A (resin) and Part B (hardener). When mixed, they undergo a chemical reaction that cures the material into a solid, plastic-like coating. Unlike paint, which simply dries by evaporation, this stuff bonds at the molecular level with your concrete. It becomes part of the slab. That’s what gives it the superior hardness, adhesion, and chemical resistance that epoxy paint just can’t match.
And we’re not just talking about durability on paper. Real-world, this means your garage floor stands up to oil spills, road salt, brake fluid, gas, and all the nasty stuff that drips off your vehicles. No bubbling. No flaking. No tire marks burning into the surface every time you pull in on a hot Little Rock summer afternoon.
Another big difference? Thickness. A properly installed 2-part epoxy system is millimeters thick—not just a film of color. You can build it up with flakes, broadcast quartz for grip, or add a urethane topcoat for UV protection and extra abrasion resistance. You’re not just painting concrete; you’re building a flooring system that’s designed to last 10, 15, even 20 years.
Most of the time, when people say, “epoxy floors are tough,” they’re talking about this system. It’s the go-to in commercial garages, warehouses, airplane hangars, and fire stations—anywhere floors need to perform under pressure. If it can handle forklifts, it can definitely handle your pickup truck and tool bench.
Now here’s the catch: real 2-part epoxy isn’t something you slap on in an afternoon. It requires serious prep—like grinding the concrete with diamond tooling, filling cracks, testing for moisture, and applying multiple coats under the right conditions. That’s where professionals come in. But the payoff? A floor that not only looks incredible, but actually performs year after year.
Side-by-Side Comparison: 2-Part Epoxy vs. Epoxy Paint
So, you’re standing in your garage, staring at bare concrete, wondering which route to take. The can of “epoxy paint” at the hardware store looks tempting—cheap, quick, and supposedly easy. But here’s where that decision either saves you money—or costs you twice as much. Let’s break it down by what actually matters when you're coating a garage floor in Little Rock.
1. Installation Process
Epoxy Paint:
Roll it on like wall paint. No grinding. Maybe some acid etching if the kit recommends it. It’s made for speed, not staying power.
2-Part Epoxy:
First step? Diamond grinding. It opens the pores of the concrete so the epoxy can actually bond. Then there’s crack repair, moisture testing, and a multi-step coating process. This isn’t a weekend warrior project—it’s a professional system that’s designed to perform.
Verdict: If you don’t prep the surface, you’re wasting time. 2-part epoxy starts with doing it right.
2. Bond Strength and Adhesion
Epoxy Paint:
Sits on top of the surface. It’s like a sticker—looks good at first, but one hot tire or oil drip and it starts to peel or stain.
2-Part Epoxy:
Chemically fuses into the concrete. It becomes part of the slab. You’d need a jackhammer to remove it if it’s applied right.
Verdict: True epoxy wins by a landslide here. It doesn’t just stick—it stays.
3. Durability & Lifespan
Epoxy Paint:
Looks decent for a year or two… maybe. Then comes the wear, discoloration, peeling, and flaking. Especially under UV or in garages with heavy use.
2-Part Epoxy:
10 to 20 years of performance when installed properly. It laughs at hot tires, oil leaks, and heavy use. It’s what we install in Little Rock auto shops, home garages, and commercial spaces.
Verdict: 2-part epoxy isn’t just durable—it’s battle-tested.
4. Chemical and Stain Resistance
Epoxy Paint:
Minimal resistance to gasoline, brake fluid, or oil. Even household cleaners can wear it down over time.
2-Part Epoxy:
Engineered to resist corrosive chemicals. Drop a wrench or spill something nasty? Wipe it up—no damage.
Verdict: If your garage sees real use, epoxy paint is out of its depth.
5. Hot Tire Pickup
Epoxy Paint:
This is the killer. Your car’s tires heat up while driving, and when you park, they pull soft paint right off the floor. It’s one of the most common complaints we hear from DIY jobs.
2-Part Epoxy:
Built to handle extreme temperatures and pressure from tires. No pickup. No peeling.
Verdict: This alone is worth the upgrade to 2-part epoxy.
6. Appearance and Customization
Epoxy Paint:
Flat color. Limited choices. Maybe it looks decent on Day One, but don’t expect it to stay that way.
2-Part Epoxy:
Glossy finishes, metallics, custom flake blends, color options galore. Want your floor to match your car, or pop with a unique design? You’ve got options.
Verdict: One looks like paint. The other looks like a custom-built floor.
7. Cost (Short-Term vs. Long-Term)
Epoxy Paint:
Yes, it’s cheaper upfront—maybe $100–$150 for a kit, plus rental tools and your weekend. But when it fails, and it will, you’ll be spending again on materials, labor, or a full tear-out.
2-Part Epoxy:
Higher upfront cost, especially if professionally installed. But it’s built to last. You’re paying for performance, not just appearance.
Verdict: You either pay now—or pay twice later.
8. Little Rock Climate Performance
Epoxy Paint:
Struggles in Arkansas heat and humidity. UV exposure from open garage doors speeds up yellowing and breakdown.
2-Part Epoxy:
Formulated to perform in real-world climates—holds up against seasonal shifts, moisture, and blazing-hot tires.
Verdict: For Little Rock garages, 2-part epoxy is built for the job. Paint isn’t.
Final Takeaway: There Is No Contest
If you’re looking for a quick cosmetic fix and you’re okay with redoing it in a year or two, epoxy paint might do the job—briefly. But if you want a floor that performs, protects, and lasts, true 2-part epoxy is the only system worth your money.
The Hidden Costs of Choosing Epoxy Paint
That $120 DIY epoxy paint kit might feel like a win at the checkout line—but here’s the part most homeowners in Little Rock don’t realize until it’s too late: epoxy paint almost always ends up costing you more in the long run. And not just in dollars.
Let’s start with the obvious. Most DIY kits don’t include the tools you’ll need to do the job right. You’ll probably have to rent a floor buffer or concrete etcher, buy degreasers, patch materials, rollers, gloves, and whatever prep gear the instructions forgot to mention. That "weekend project" just turned into a car full of gear and a busted Sunday afternoon.
But even if you check all the boxes and follow the instructions to a T, the real kicker comes later—when the paint starts to fail.
At Rock City Epoxy, we get calls all the time from homeowners who tried the DIY route a year or two ago. It’s always the same story:
"It looked great at first, but then the tires started pulling it up."
"Now there are patches where it’s flaking off."
"Every time I sweep, more of it comes loose."
And here’s where it gets expensive. Once that paint fails, you can’t just coat over it with real epoxy. Nope. You have to strip it—every last bit. That means grinding down the failed coating, repairing the damage it left behind, and starting fresh. You’re paying for removal, repair, and a brand new install.
Worse? Some paints soak into the concrete unevenly, making prep even more time-consuming (and costly). So that $120 project just added hundreds—maybe thousands—in labor and materials.
And it’s not just about money. There’s downtime, too. You’ll need to empty your garage again, stay off the floor during repairs, and deal with the hassle of fixing something that shouldn’t have failed in the first place.
There’s a saying in this industry: “Cheap epoxy jobs are expensive epoxy problems waiting to happen.” And nowhere is that more true than with DIY epoxy paint.
Why We Only Use 2-Part Epoxy at Rock City Epoxy
Here’s how we see it—if we’re putting our name on your garage floor, it better last. That’s why at Rock City Epoxy, we don’t touch 1-part epoxy paint. Not for garages. Not for shops. Not even for low-traffic areas. Why? Because we know how Arkansas garages really get used—and we know what actually holds up.
When you hire us, you’re getting a real-deal flooring system, not just a coat of color. Our process starts with surface prep, and we don’t cut corners. We use commercial-grade diamond grinders to open up the pores of the concrete, ensuring our 2-part epoxy actually bonds deep into the slab. This is critical—paint won’t stick if the floor isn’t properly profiled. And acid etching? It’s not enough. We grind because it works.
Once the surface is prepped, we repair cracks and spalls, test for moisture, and make sure we’re not laying anything down on a compromised surface. That step alone saves countless floors from failure.
Then comes the fun part—layering the system:
A high-build primer coat for maximum adhesion.
A 100% solids epoxy base coat (the real muscle).
Decorative flakes or quartz broadcast, if you want texture and style.
A UV-stable urethane or polyaspartic topcoat, depending on your environment.
The result? A floor that’s tough, chemical-resistant, and built to handle everything from lifted trucks to engine oil, lawn equipment, and Arkansas humidity. Whether you’re in Little Rock, North Little Rock, Conway, Benton, or Bryant, we deliver floors that work as hard as you do.
We don’t believe in one-size-fits-all coatings. Every garage has different needs, and we tailor our system accordingly. The one thing that never changes? We always use true 2-part epoxy. Because shortcuts might work for a minute—but we’re here to build floors that last for years.
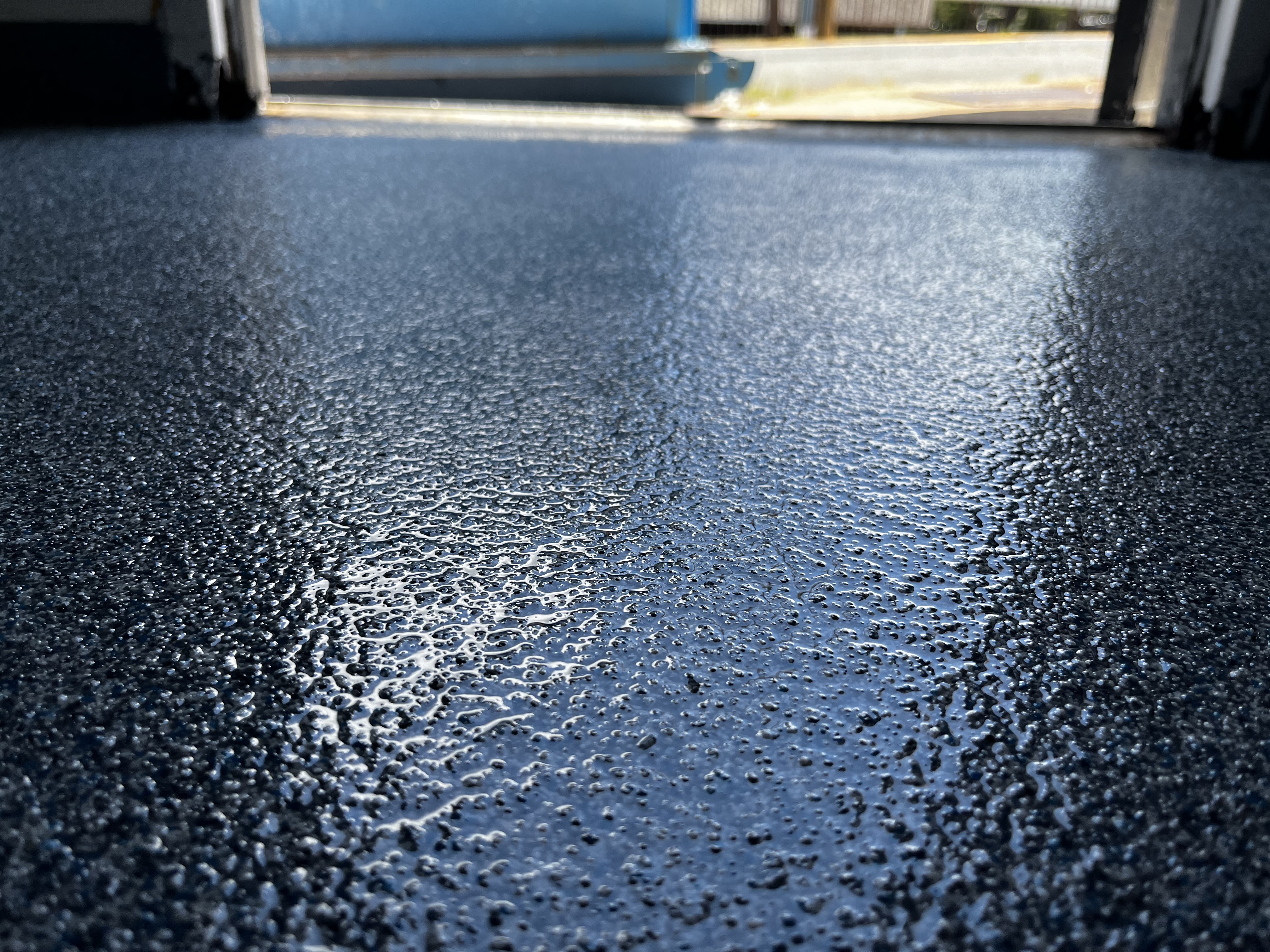
When Might Epoxy Paint Make Sense? (It’s Rare, But Let’s Be Honest)
We’re not here to knock every single can of epoxy paint on the shelf. There’s a time and place for it—just not in high-traffic garages that see real action. But if we’re being honest, there are a few scenarios where epoxy paint might make enough sense to justify the risk.
1. You’re selling the house and want a quick refresh.
If you’re prepping for a sale and just want the garage to look a little cleaner without a long-term investment, epoxy paint can give you that short-term shine. It won’t hold up under heavy use, but for curb appeal? It gets the job done—briefly.
2. You’re coating a storage space, not a working garage.
If your garage is more like a glorified storage unit and doesn’t see vehicles, tools, or fluids, epoxy paint may be “good enough” to cover old concrete and brighten up the space. Just don’t expect it to handle rolling tool chests or dripping oil.
3. You’re experimenting.
Let’s say you’re a DIY enthusiast and you know the limitations. You want to see what you can do with a $100 kit before committing to a professional install. That’s fair—as long as you go in with your eyes open and don’t mind redoing it down the road.
But here’s the reality check: even in these cases, you’re gambling. Epoxy paint still needs surface prep to stick, and most people skip it. If it fails, you’re back to square one—and now the concrete’s contaminated with a flaky mess that makes future coatings harder to apply.
Bottom line? You can make epoxy paint work if your expectations are low and you understand what you’re getting. Just don’t confuse it with the real thing.
Final Verdict: If You’re Coating Concrete, Go All In or Don’t Bother
Here’s the deal: garage floors in Little Rock aren’t just decorative. They take heat, pressure, chemical abuse, moisture—you name it. So when you’re deciding how to protect that concrete, it’s not just about how the floor looks the day after it’s done. It’s about how it performs for the next five, ten, or twenty years.
1-part epoxy paint might look like a shortcut, but it’s really just a temporary Band-Aid. It sits on top, it doesn’t bond deep, and it fails fast. Especially under hot tires, tool traffic, or humid Arkansas summers.
True 2-part epoxy? That’s the system that lasts. It bonds chemically with your concrete, creates a high-performance surface, and gives you serious options in terms of style, texture, and durability. It’s the difference between a quick coat of paint and a true flooring solution.
So ask yourself: Are you just trying to cover up your garage floor—or are you ready to upgrade it?
Because if you’re serious about doing it right the first time, you already know the answer.
Let’s Talk About Your Garage
If you’re tired of peeling paint, hot tire marks, or floors that just don’t hold up, it’s time for something better. At Rock City Epoxy, we install garage floors that don’t just look good—they perform. Whether you’re in Little Rock, North Little Rock, Conway, Benton, or anywhere in Central Arkansas, we’re here to help you get it done right.
Call TJ at 501-408-6160
email [email protected]
or fill out our contact form to get a free quote and find out what system is best for your space.
You’ve got better things to do than recoat your garage every couple of years. Let’s make this the last time you ever have to think about it.
Click here to read more about our epoxy flooring systems